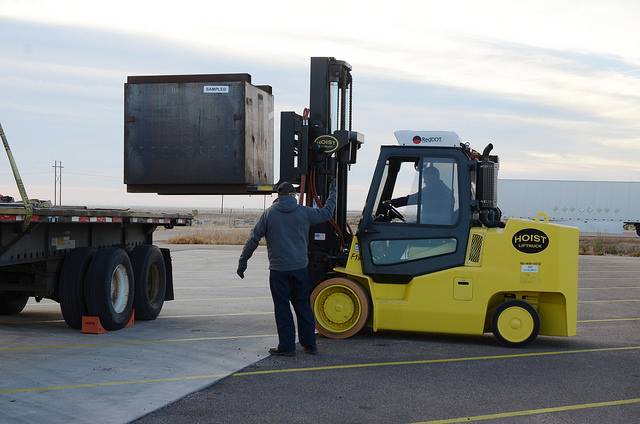
Has there been a recent scourge of accidents in the workplace that have resulted in catastrophic losses and an increase in injuries? Do you find yourself puzzled as to how they occur and where to begin to repel them? The truth of the matter remains that workplace accidents are an extremely costly event. Whether it be ranging from a loss in productivity to legal costs, these incidents can affect the time, the efficiency, and the bottom line of any enterprise from top to bottom. The good news is there are some basic actions you can take to prevent them. Here is more on how costly workplace accidents can have truly detrimental effects:
- Loss In Productivity – Workplace accidents are proven to slash productivity. This can be chalked up to a wide range of reasons. First and foremost, an accident is likely to result in a loss of tools and components essential to achieving the objective in specified timeframes. Even worse, accidents can result in injuries which means teams will be short-handed in completing the project. As a result, this will translate to longer timeframes to execute said initiative. However, the implementation of telematic systems has been a great way to be proactive in preventing accidents while also assessing performance analytics. These interfaces allow any owner to identify systemic bottlenecks which in turn boosts productivity across the board.
- Maintenance and Equipment Costs – As mentioned in the first bullet point, maintenance and equipment costs are often a direct effect of a workplace incident or accident. Whether it be a malfunction, mishandling, or general wear and tear as the cause, these expenditures can be mountainous. However, routine and preventative maintenance on all vehicles and appliances can isolate areas of risk in usage and determine repair needs before they manifest into a more prolific trouble. Monitoring and moderating your fleet is another proactive preventative action.
- Legal Costs – More often than not, these events result in a hike in legal costs. In today’s world, it’s also more likely than ever that the worker will hire an accident lawyer to represent them. Whether it be as a result of civil litigation or workman’s compensation claims, the prevalence of such affairs results in the requirement to hire law services to deal with the matter. According to Total Trax, identifying potential accidents before they occur is a sure-fire way to diminish the likelihood of accruing these costs. For example, it is estimated that over 20,000 workers are injured in forklift accidents on an annual basis. Implementing comprehensive forklift training would be a sound strategy in quelling those incidents while also bolstering required skills.
- Salary of Injured Worker – In many instances the end result of these situations is any business picking up the tab for owed salary for the injured worker. In fact, is approximated that the average accident can result in over $35,000 in employee wages being shelled out as a result of these scenarios. As a result, these enhanced losses can substantially lower profits if the employee in question is an integral part of the material handling or production process. Promoting continuous improvement in safety awareness is an excellent approach to staying ahead of the curve when it comes to hazard identification.
Author Bio
Claim up to $26,000 per W2 Employee
- Billions of dollars in funding available
- Funds are available to U.S. Businesses NOW
- This is not a loan. These tax credits do not need to be repaid
Tom Reddon is a forklift specialist and blog manager for the National Forklift Exchange. He also sits on the Material Handling Equipment Distributors Association (MHEDA) Executive Dialogue team. Follow him on Twitter at @TomReddon.